Before pressing can begin, a die must be created with the design of the areas we intend to stamp with foil. Although invisible to those who interact with our products, the die is crucial to the foil stamping process, shaping our designs into tangible products.
#05
ROKKAKU StoryThe Road to a Single Stamp Vol. 3
〈The final push at the end of a long, laborious process〉
Stamping with foil
Just like that, foil stamping transforms the surface of paper with a textured imprint and a glossy finish that ink printing simply cannot achieve. However, arriving at this stage involves numerous steps that demand careful consideration and expertise, including design, foil selection, die production, and press setup.
What kind of process brings out the full brilliance of the foil and infuses additional color into a design? Let’s explore the detailed journey that culminates in a luminous final product.
ー
After the design and foil are selected, the next step is pressing the stamp. While it might seem that the hard work is done, a complex and meticulous process still awaits. This is the stage where skilled craftsmanship truly shines, as it brings the elaborate designs and chosen foils to vivid life.
Index
-
01
The all-important die that joins the foil to the paper
-
02
The right press for the design
-
03
Millimeter-level positional alignment
-
04
Setting the temperature and pressure according to the foil, paper quality, and climate
-
05
COMMENT
The all-important die that joins the foil to the paper
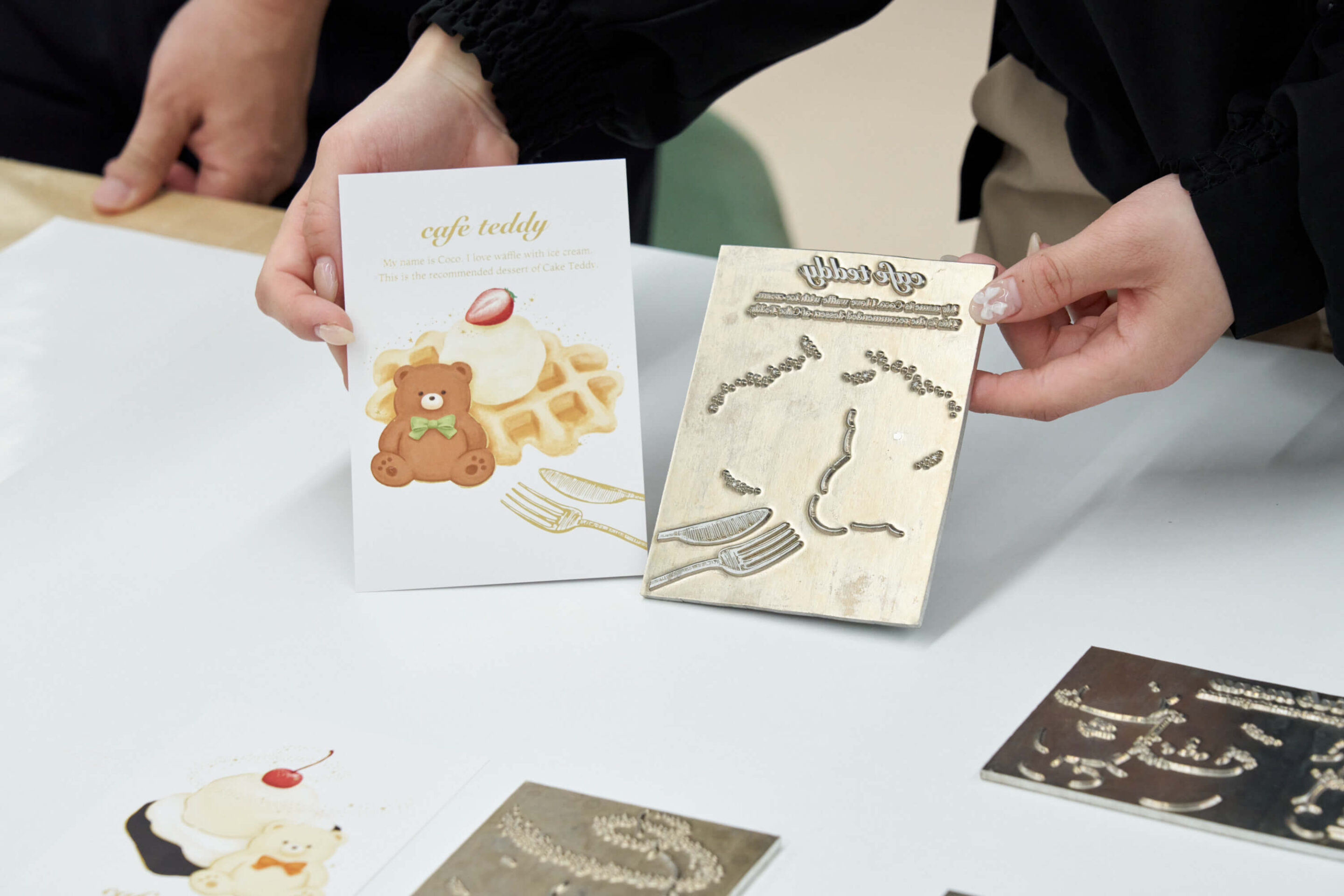
The die is meticulously engraved with the design’s contours and textures, with the areas for foil stamping prominently raised. It transfers the foil to the paper through a combination of high temperature and pressure.
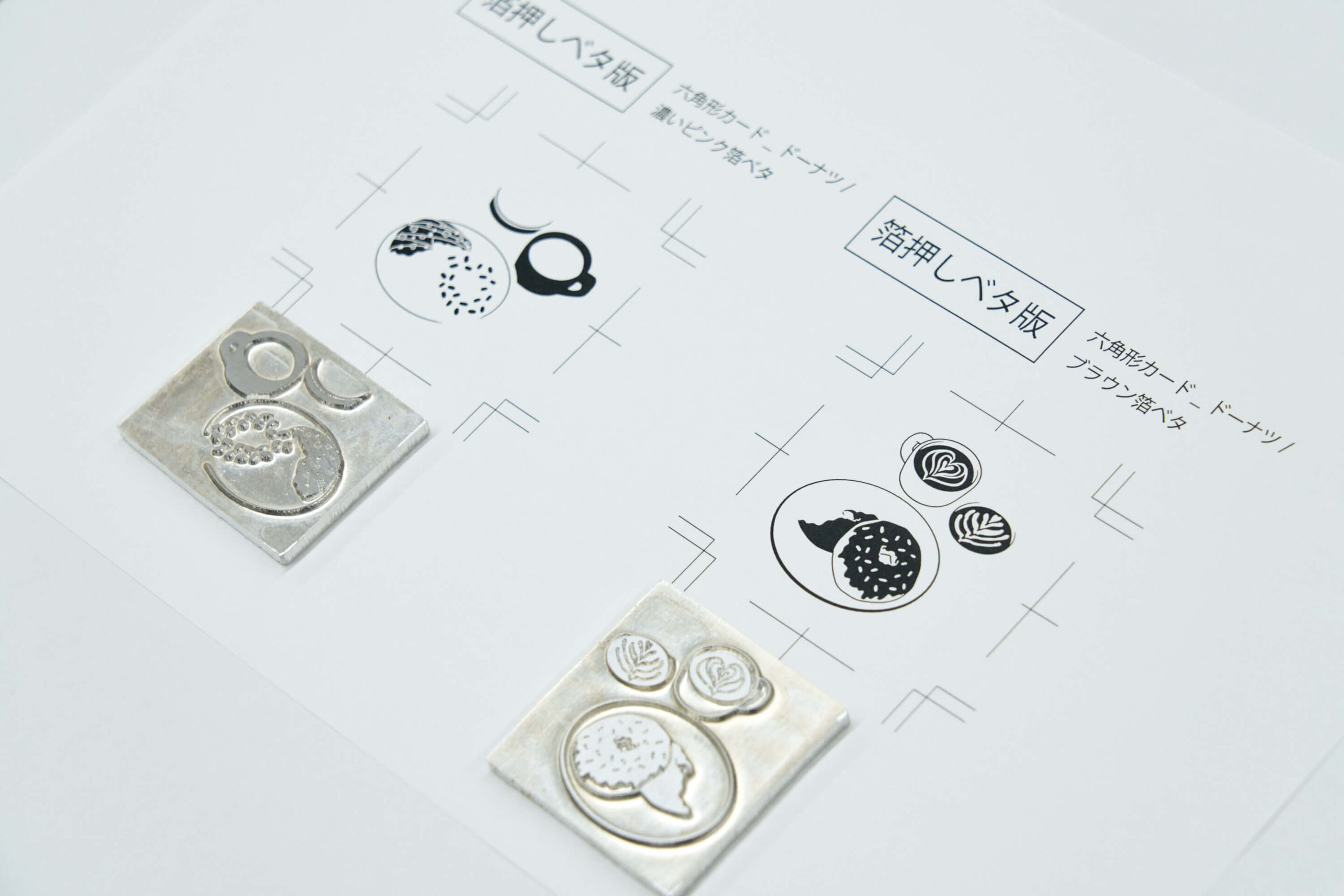
These dies are crafted from designer-created data that ensures both aesthetic appeal and technical viability. Although the design data is verified for accuracy before die production begins, the true test of its effectiveness comes during the actual stamping process. Once the paper, foil, and dies are prepared, the stamping process commences.
The right press for the design
At ROKKAKU, our in-house foil stamping shop facilitates the entire process from design to production under one roof, allowing for seamless communication between designers and production staff to enhance quality.
Our shop is equipped with various presses, including both manual and automatic models, selected based on the product size and processing needs.
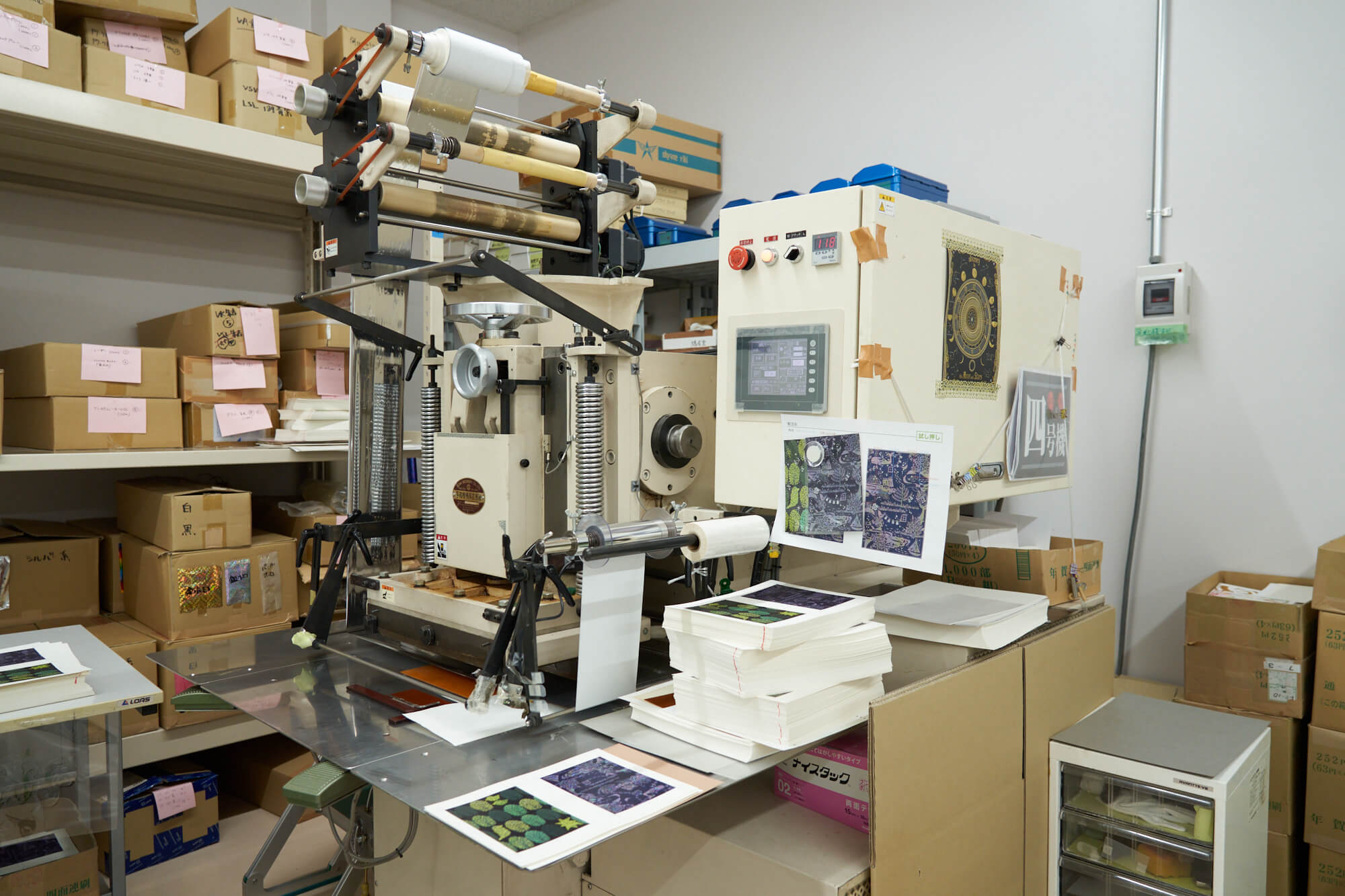
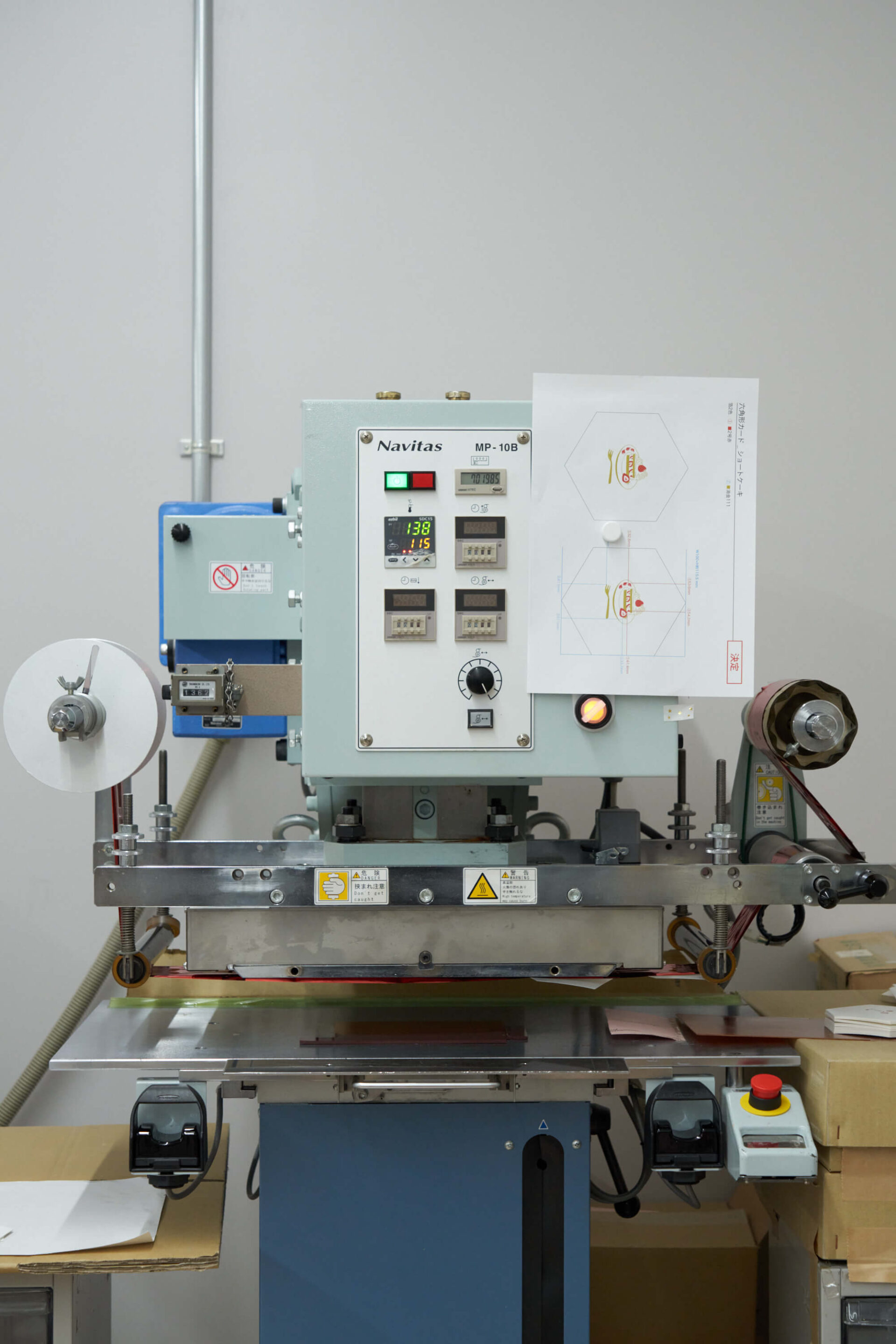
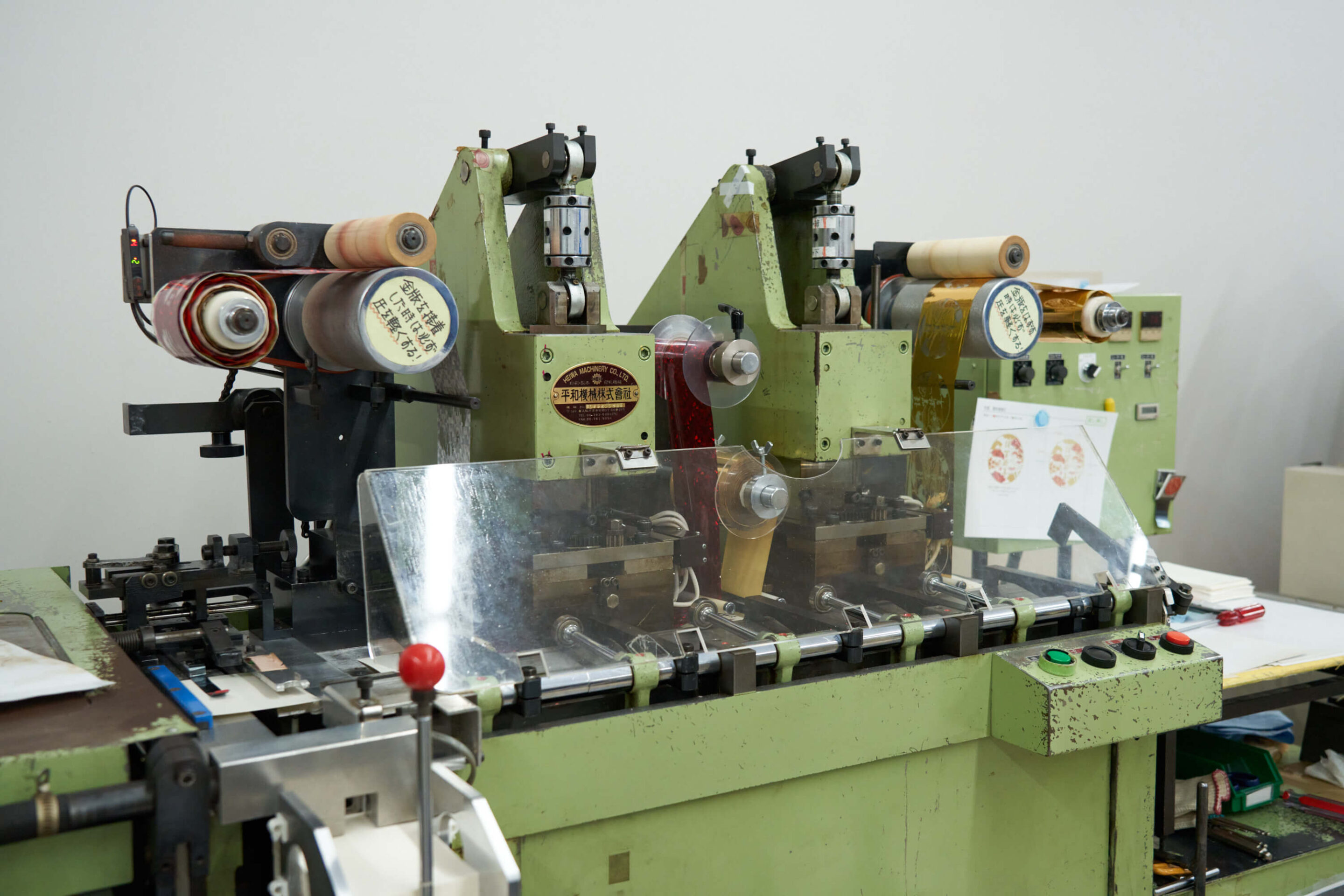
While the types of presses vary, they all operate on the same fundamental principle, using heat and pressure to apply the foil. The next step involves finely tuning the press settings to achieve the desired results.
Millimeter-level positional alignment
The first step in setting up the press is meticulously aligning the components. Precision is crucial; even a minor misalignment of about 0.1 mm can significantly alter the appearance of the final image.
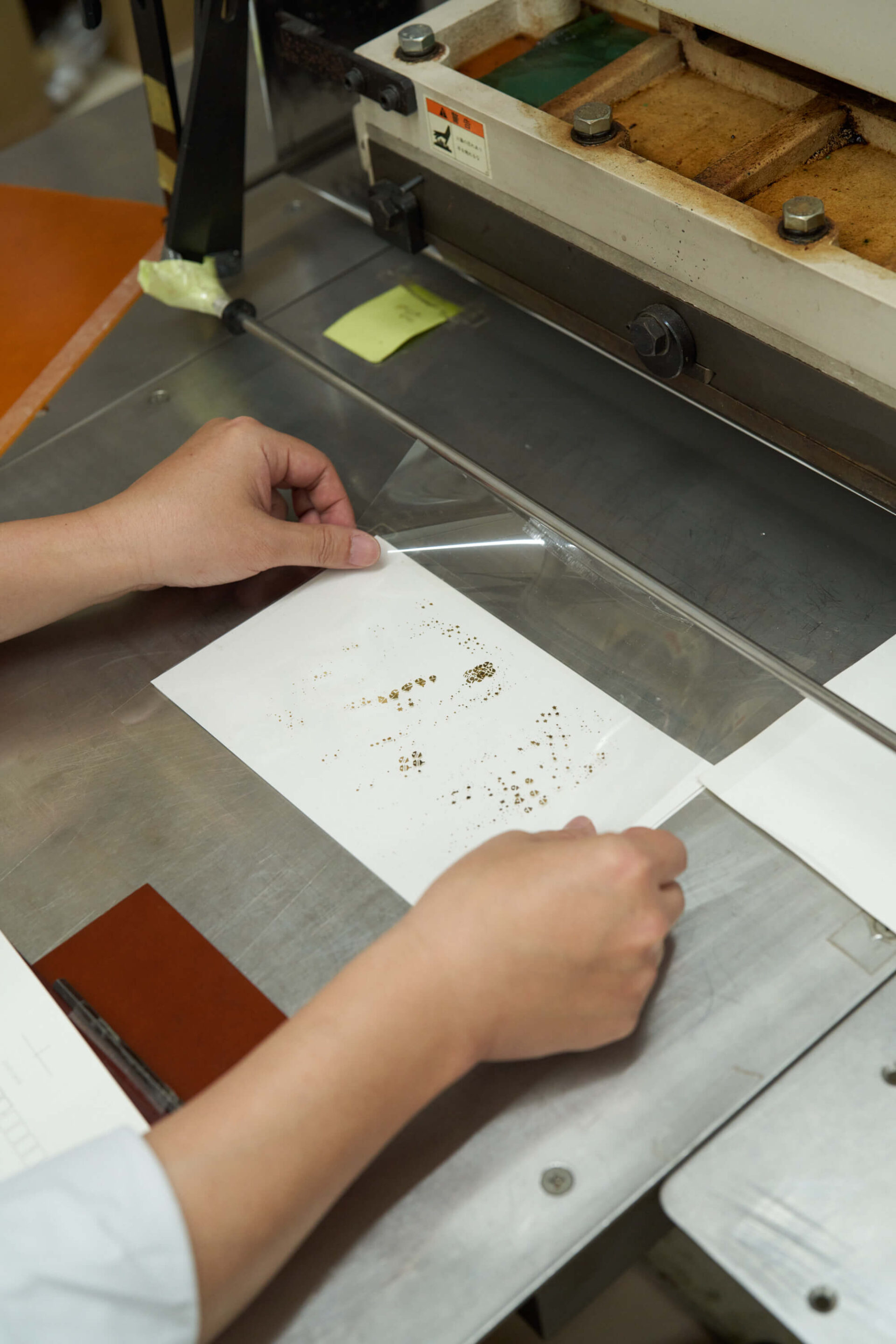
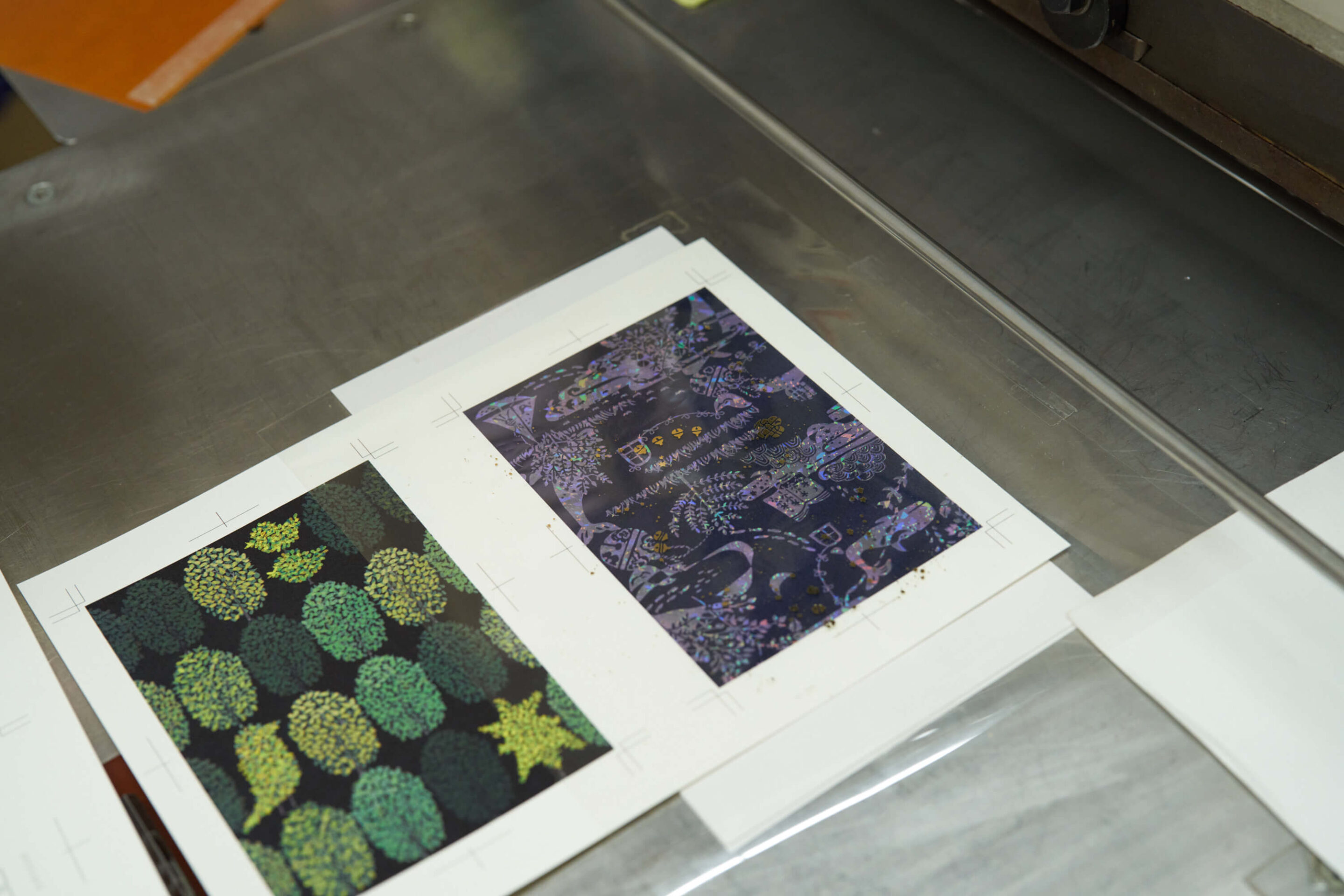
If a design is complex, involves multiple dies, or includes overlapping foils and patterns, any misalignment becomes particularly noticeable, demanding extra time and precision in press setup. While simplifying the design could ease the pressing process and reduce misalignment risks, the intricate details are a hallmark of ROKKAKU’s uniqueness. Therefore, expert alignment by skilled craftspeople is vital.
Setting the temperature and pressure according to the foil, paper quality, and climate
Even once everything is perfectly aligned, we’re not quite ready to press. First, critical adjustments must be made to the temperature and pressure settings. Foil stamping involves transferring foil onto paper through high pressure and temperature, which are not constant values but vary depending on the foil type, paper quality, and even the ambient humidity.
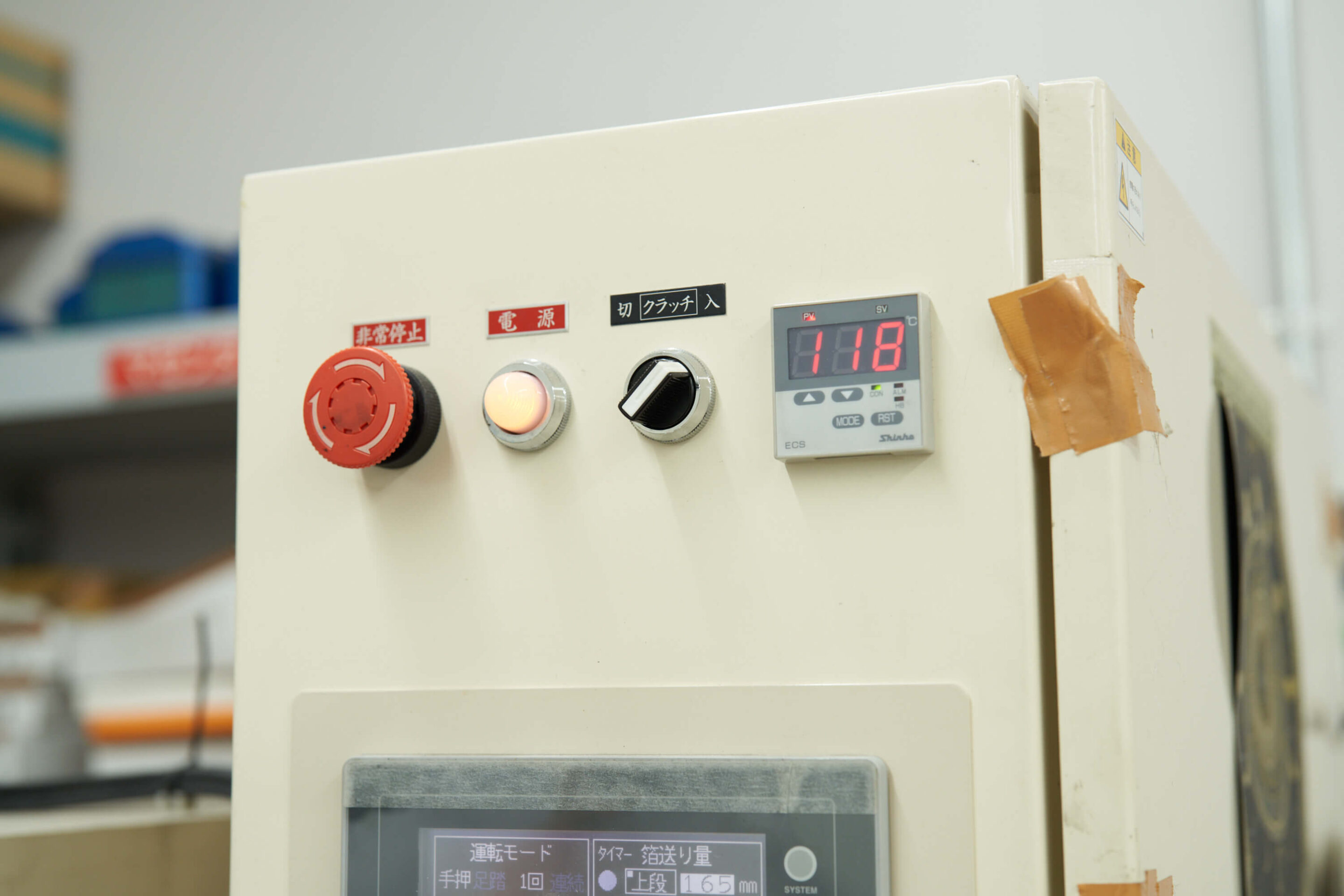
Furthermore, since the foil’s adherence varies between textured and smooth paper areas, it’s essential to finely tune the temperature and pressure to ensure the foil uniformly adheres across the entire surface. This task becomes more challenging with larger stamping areas, as the entire surface requires even pressing.
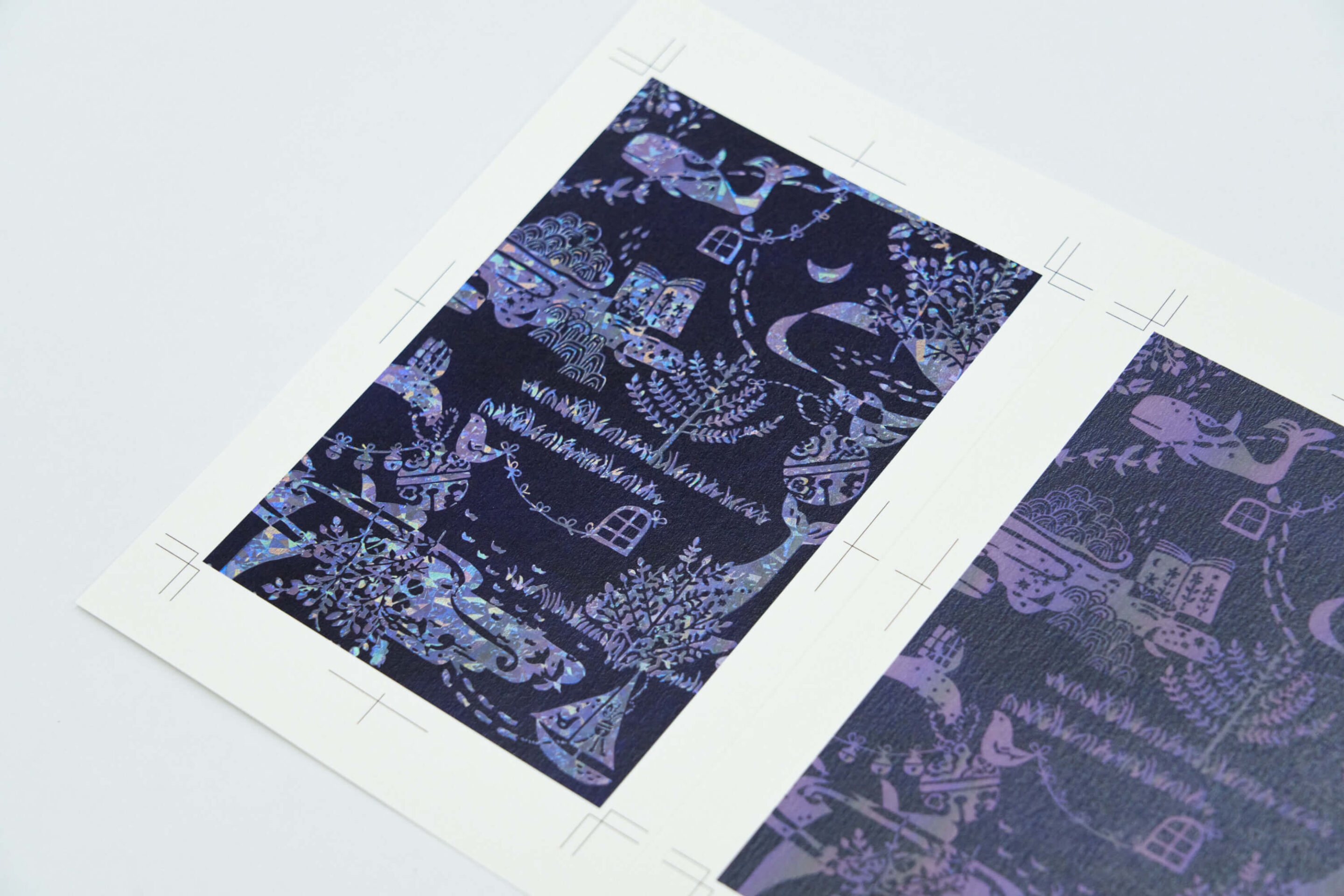
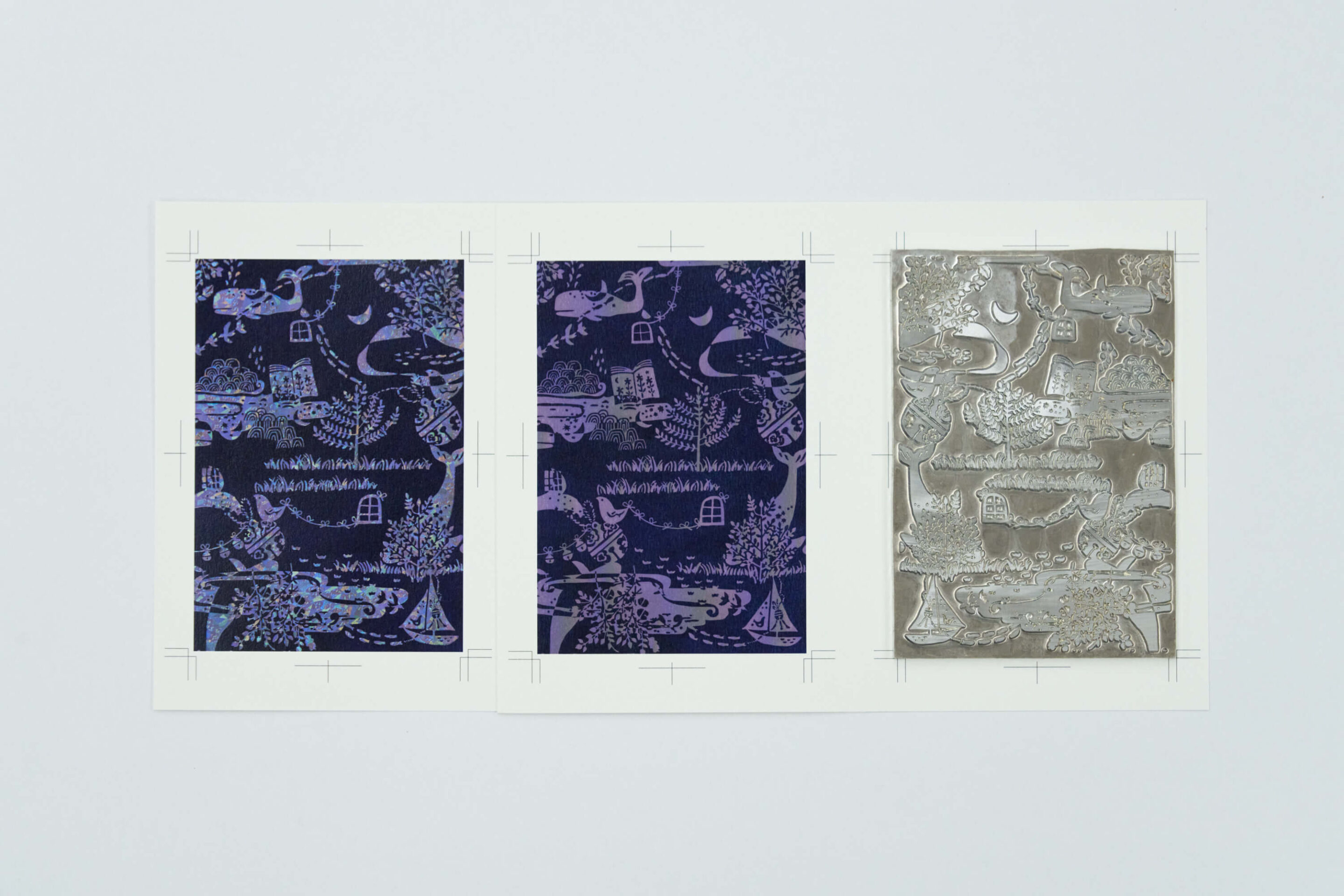
Detailed impressions require significant temperature and force. The temperature typically reaches around 120°C, with the pressure set at five tons for an automatic press and between 10 to 30 tons for a manual press. We also meticulously adjust the pressing time in 0.1-second increments. Over-pressing can imprint an outline on the back of the paper, while under-pressing may cause blurring and unevenness.
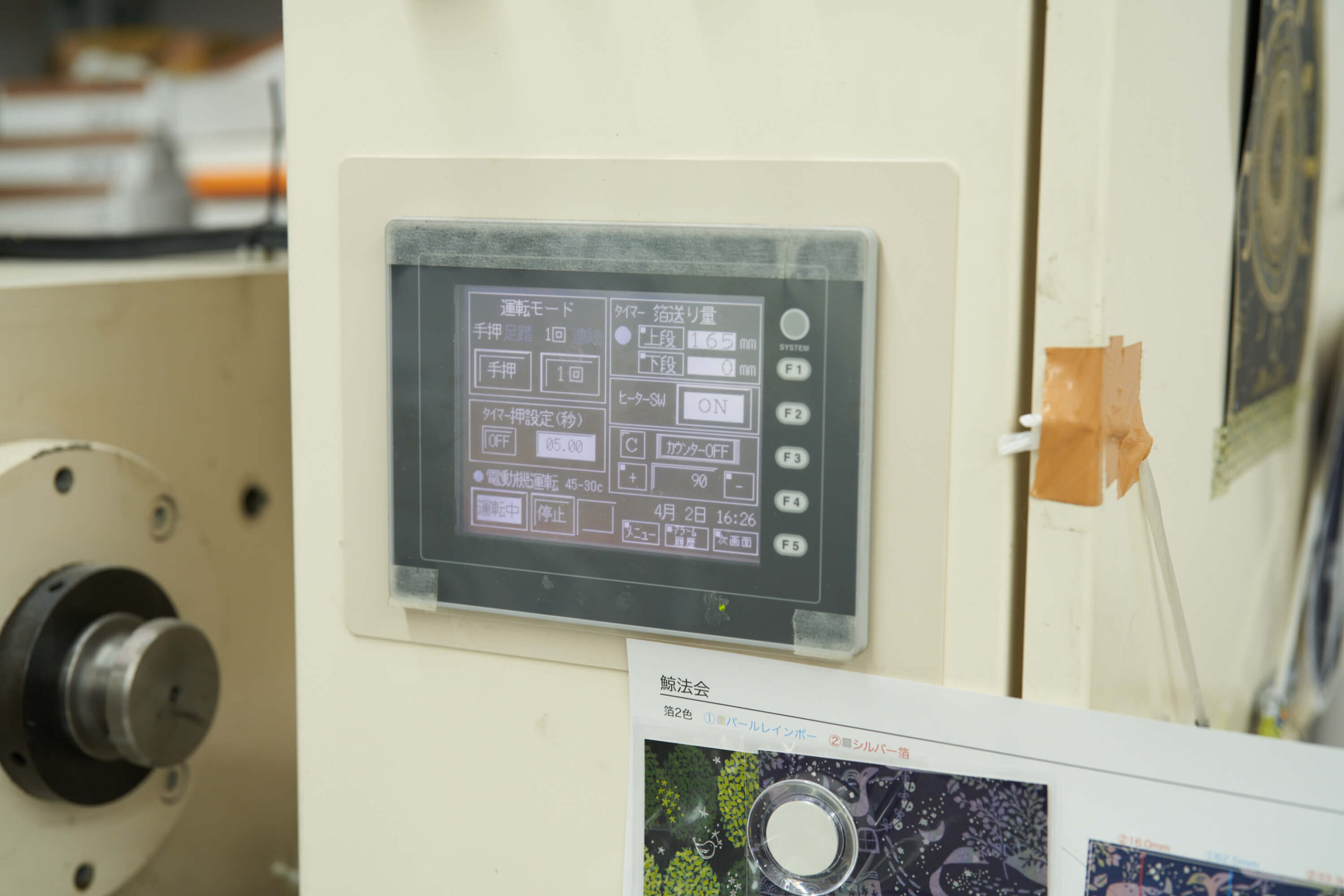
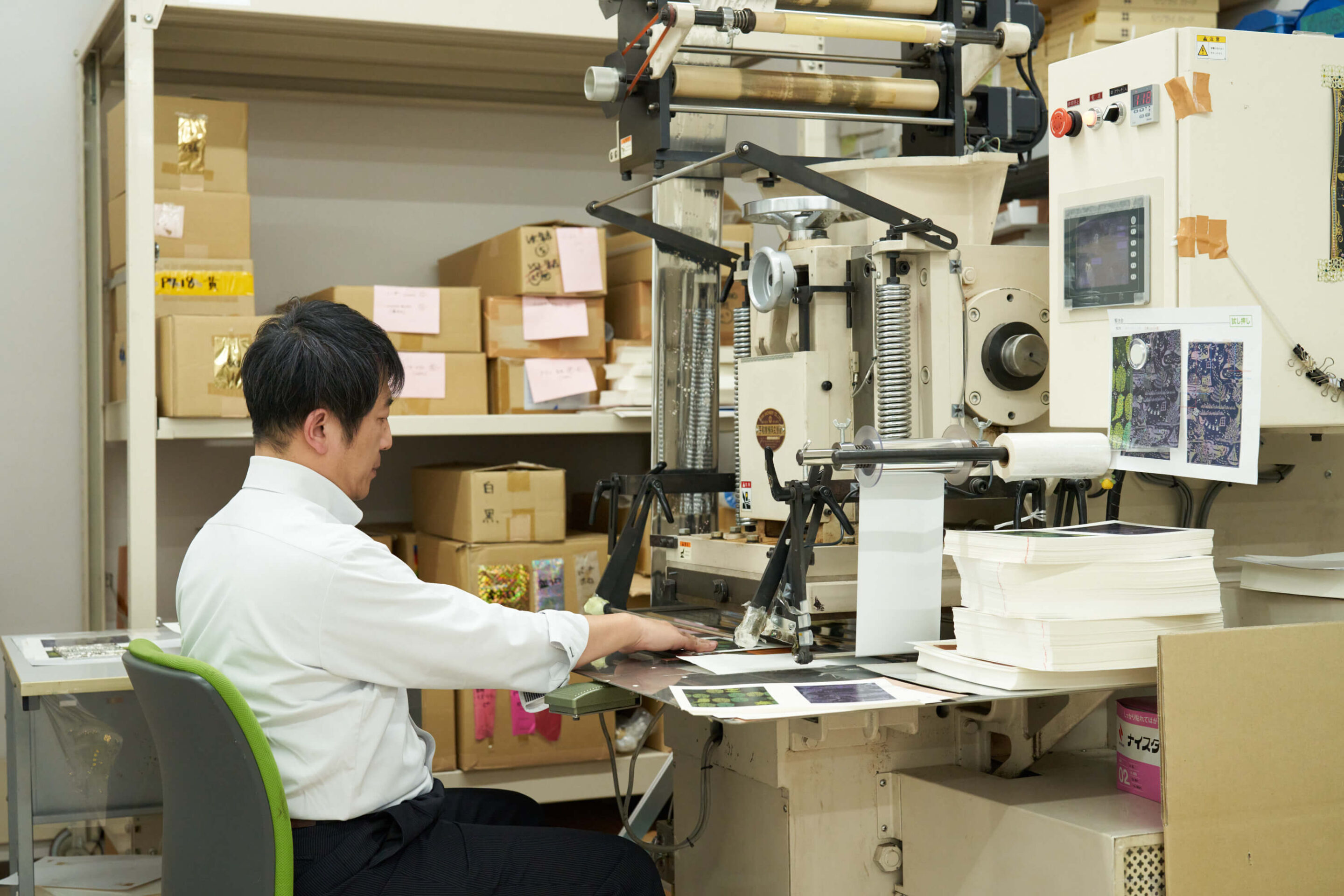
Position, temperature, pressure, and time—all these factors are carefully considered. After making precise numerical adjustments, we establish the optimal settings for the die to be pressed.
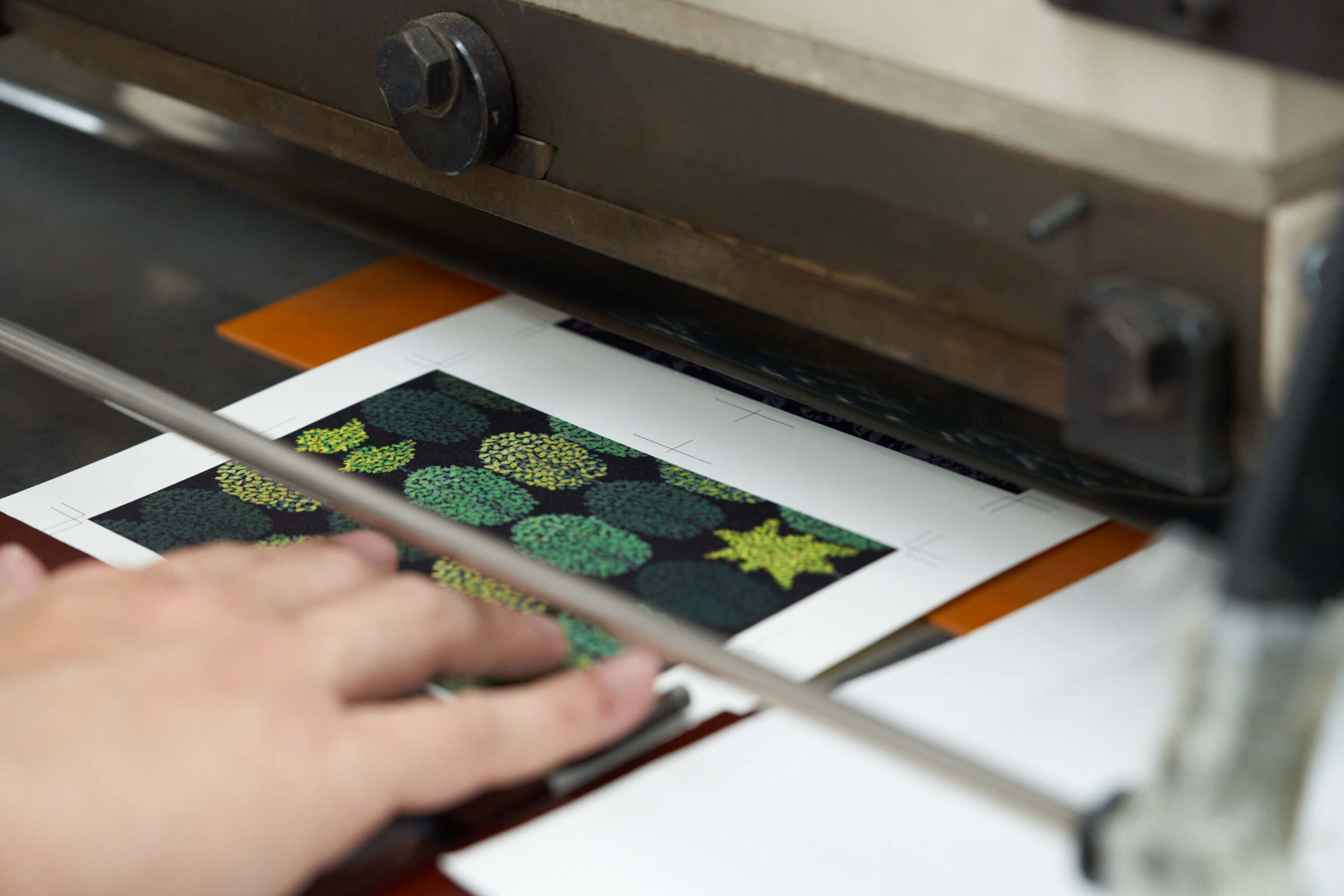
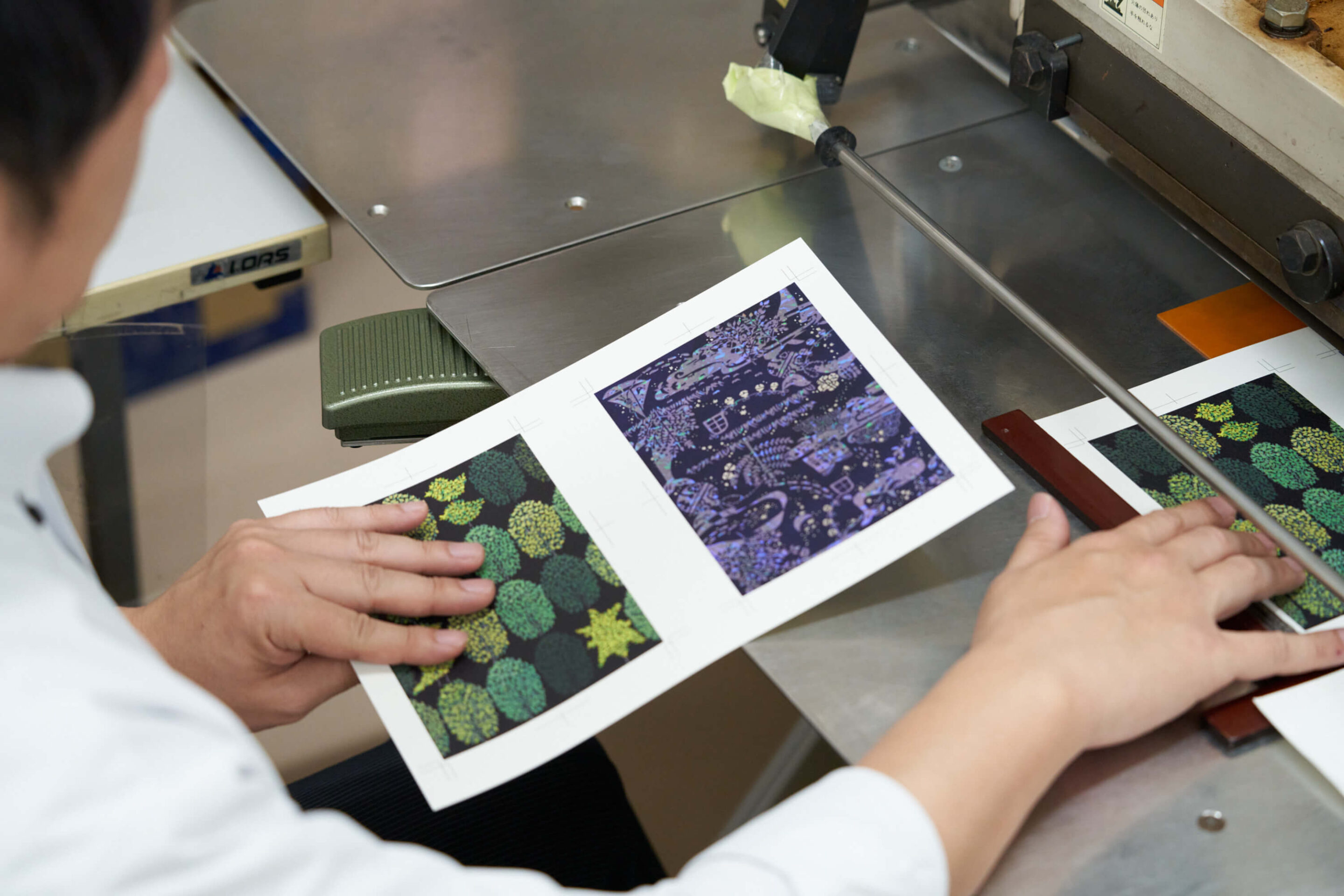
The die emits a heavy sound as it stamps the paper. The process culminates when the paper is carefully removed from the press. As expected, the foil is perfectly positioned and firmly adhered to the paper. Reflecting on the months of work from initial design to this final stage, the foil appears even more radiant. The foil stamping process concludes with the rewarding moment of holding the completed product.
COMMENT
Finally, we gathered feedback from two team members responsible for designing and operating the presses for foil stamping.
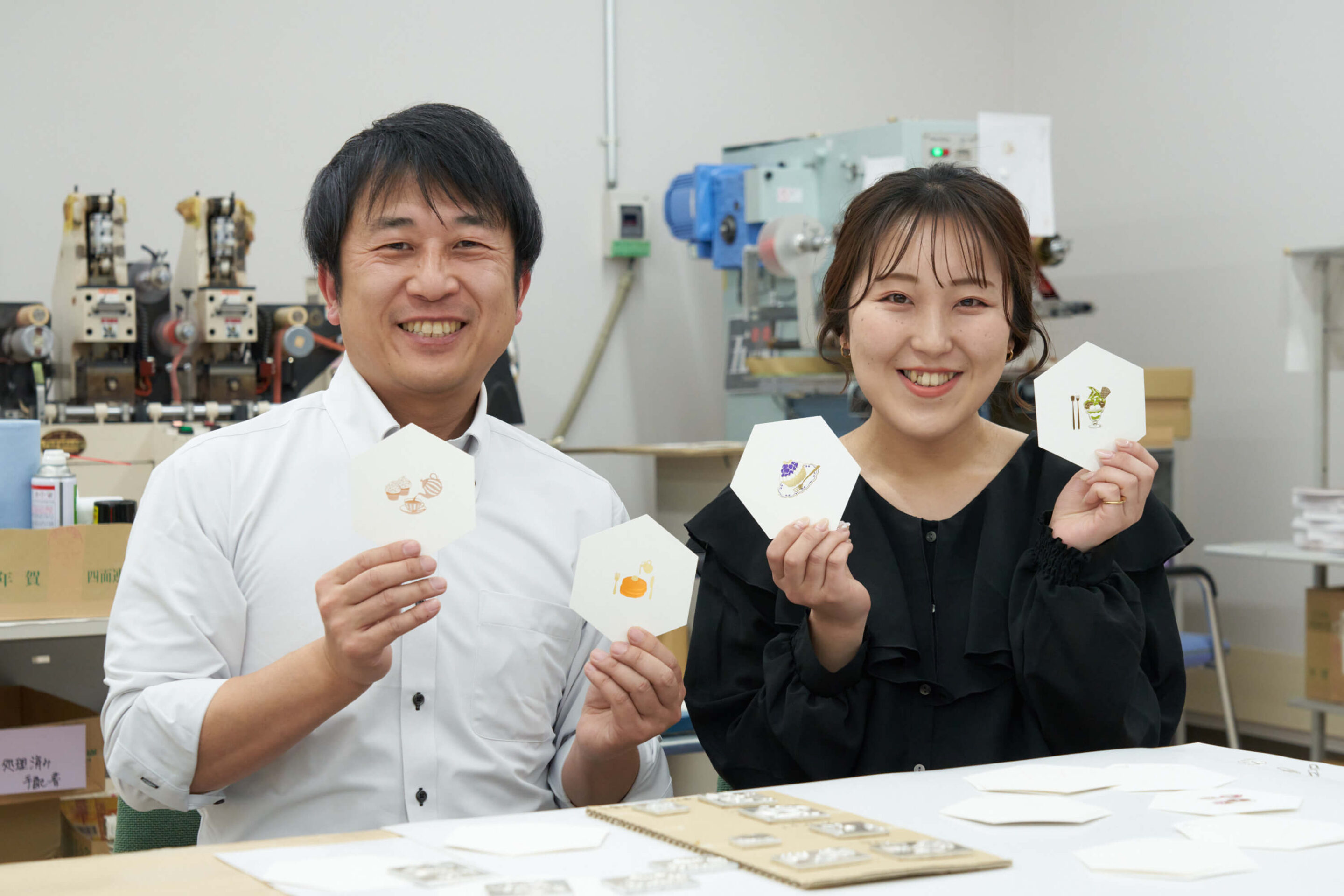
——What is important to you when working with the press?
“If the foil stamping doesn’t turn out as expected, I sometimes have to tweak the design. Altering the design can shift its original intent, so I usually try to push the press to its limits to find a solution. The reality is, I don’t know if it will work until I actually press the button. It’s challenging, but overcoming these difficulties is incredibly satisfying and truly tests my skills.”
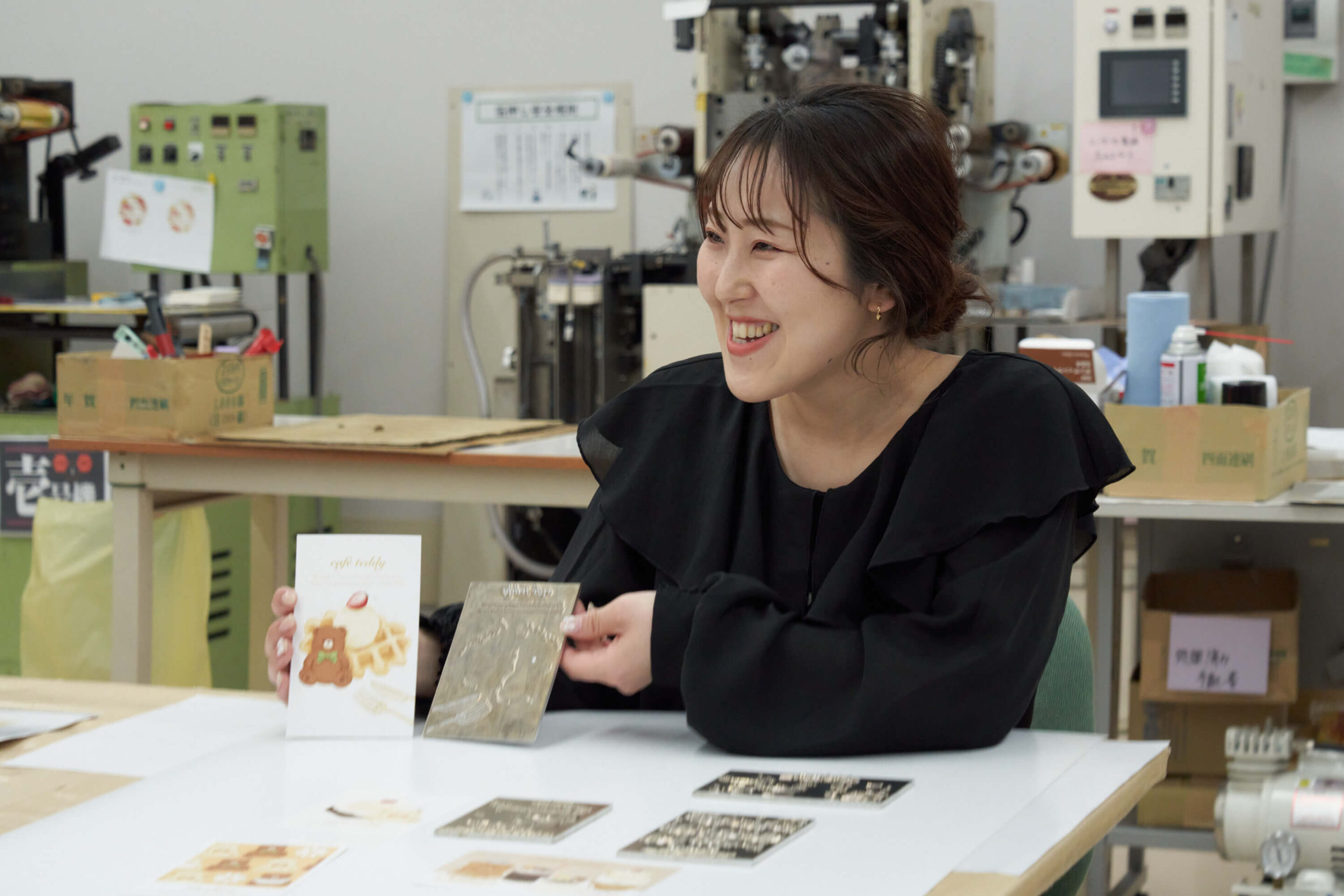
—— What do you think is the appeal of foil stamping?
“The most gratifying moment is perfectly aligning the foil stamping. Once the design and foil are set, the remaining task is the pressing process. However, a lot of time and effort goes into adjusting for issues like misalignment and blurring from temperature and pressure variations. We could settle for less than perfect, but given the effort invested in the design, we always aim for perfection. The true beauty of foil stamping lies in how the final product reflects the meticulous care put into its creation.”
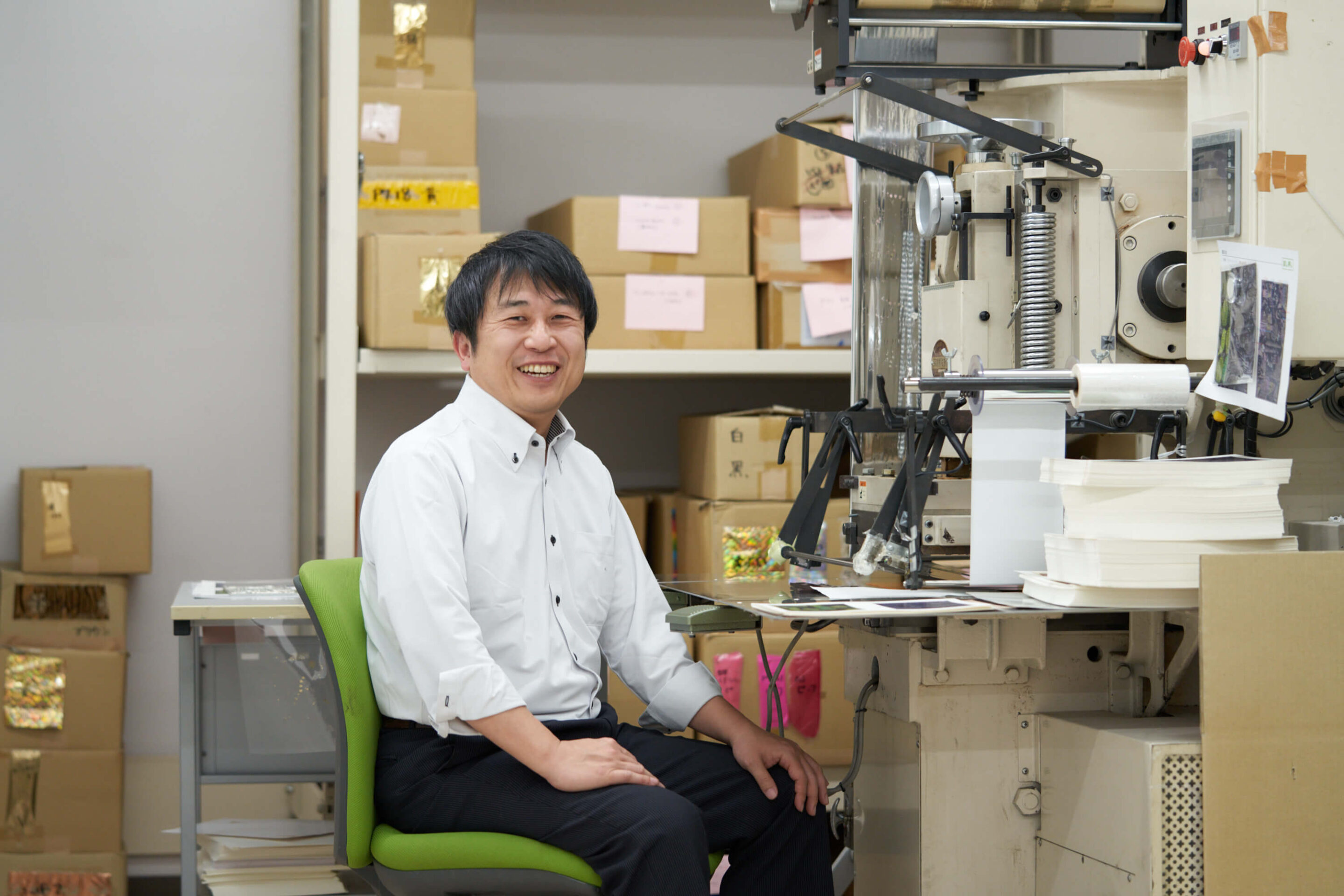
The design, foil selection, and pressing process—over three articles, we’ve delved into the complexities of foil stamping. Behind its shimmering finish lies a meticulous and strenuous journey. It all culminates with one press, but the impact of seeing the final product, knowing the extensive work behind it, is profound. Experience this excellence firsthand with ROKKAKU’s products.